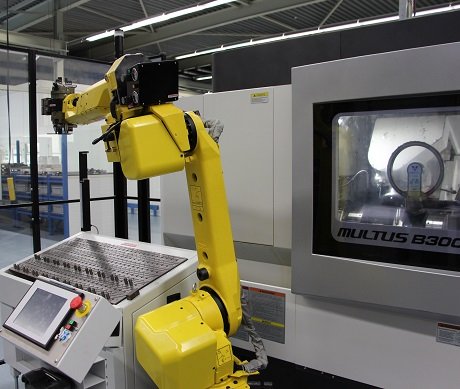
IGS GeboJagema
IGS GeboJagema
IGS GeboJagema
IGS GeboJagema is a Dutch company with a rich history. It was founded in 1945 in Tilburg, where it started as a supplier of Instruments, Tools (in Dutch, Gereedschappen) and Stamps (in Dutch, Stempels) - abbreviated to IGS in Dutch. Over the years, the activities were expanded. Today, IGS GeboJagema purely supplies tools and moulds. It is, as we know, a challenge to remain financially healthy in this highly competitive sector, thus choices have had to be made. IGS GeboJagema chose to focus on the medical market, which is in fact more quality-driven and less price-sensitive. Moreover, the life cycles of medical devices are very long, and thus more emphasis is put on the relationship between the customer and the supplier in the longer term.
Not an obvious mission as it quickly turned out. But through the acquisition in 2011 of HTP Tooling in Eindhoven, doors were opened which had previously been closed. Indeed, the capacity was increased considerably, and so IGS GeboJagema grew to become an interesting supplier for national and international players in the Healthcare market. The integration between HTP Tooling and IGS GeboJagema has therefore proved to be a good move: IGS moved in with HTP in Eindhoven and there the new colleagues found each other in the building where the two machine parks were also combined.
GlaxoSmithKline was soon pulled in as a new customer, convinced by the modern machine park and the enormous capacity. Since 2011, that machine park has also been completely renovated and replaced. Since then IGS GeboJagema has had a growth that many other companies can only dream of. What also catches the eye is that the growth has been achieved with only 2 additional employees in production. The rest is due to the ultra-modern machinery and automation.
Hans Arts, Head of Sales & Marketing: “The way of working appears to be the key to success for us. However, you don’t just get there with only a machine park and automation. The employees also have to believe in the story: the way they work is completely different from a few years ago. For example, previously we used to have quite a lot of activities: milling, grinding, electrical discharge machining, wire spark erosion,.. Some 12 or 13 different processing operations. Now there are just 4 activities: Soft steel manufacturing, Hardened component manufacturing, Grinding and Assembly. We now also work completely ‘paperless’. And thanks to automation, the quality of our finished components is so good and so consistent, that we do much more assembly work with the same number of employees as previously. We have thus become significantly more efficient."
This also bears fruit: customers in the Healthcare market from around the world are now finding their way to Eindhoven, and IGS GeboJagema has succeeded in stabilizing its client portfolio.
Automation seems to already have been a given at IGS GeboJagema for a number of years and likewise, modern machines. Three years ago, an Okuma Multus B300-II W was acquired, with enhanced accuracy on the milling-shaft. Three employees were chosen to get to learn all about this new machine for a whole year. The capabilities of the Multus B300 II WE are unprecedented: this machine can turn, mill, drill round, engrave,.. After having become acquainted with the machine for a year, it ran for 40 to 50 hours per week. It was then decided to automate this machine with a Turn-Assist Essential from RoboJob. Since then it’s been operating for 80 to 90 hours per week.
“Our director Peter Mertens himself purchases all machines. He had already heard about RoboJob and went to see them in their showroom in Heist-op-den-Berg. Peter has learned the craft in the workplace himself. He started his career at IGS as a grinder and when it comes to machining there’s nothing he doesn’t already know. Not surprisingly Peter quickly saw the strengths in the Turn-Assist, and that this automation really was developed on the work floor. For us, the way of working took some getting used to, but now we now always work with pallet loading. The choice for RoboJob was therefore a conscious choice for workpiece loading. And we’ve not regretted that, even for one second. Using the Turn-Assist Essential we always make series of 15, 20 or up to 30 pieces. The setup time is therefore crucial: RoboJob was able to demonstrate to us that they are by far the best in this."
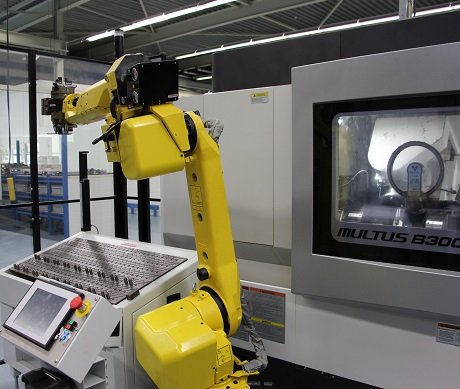