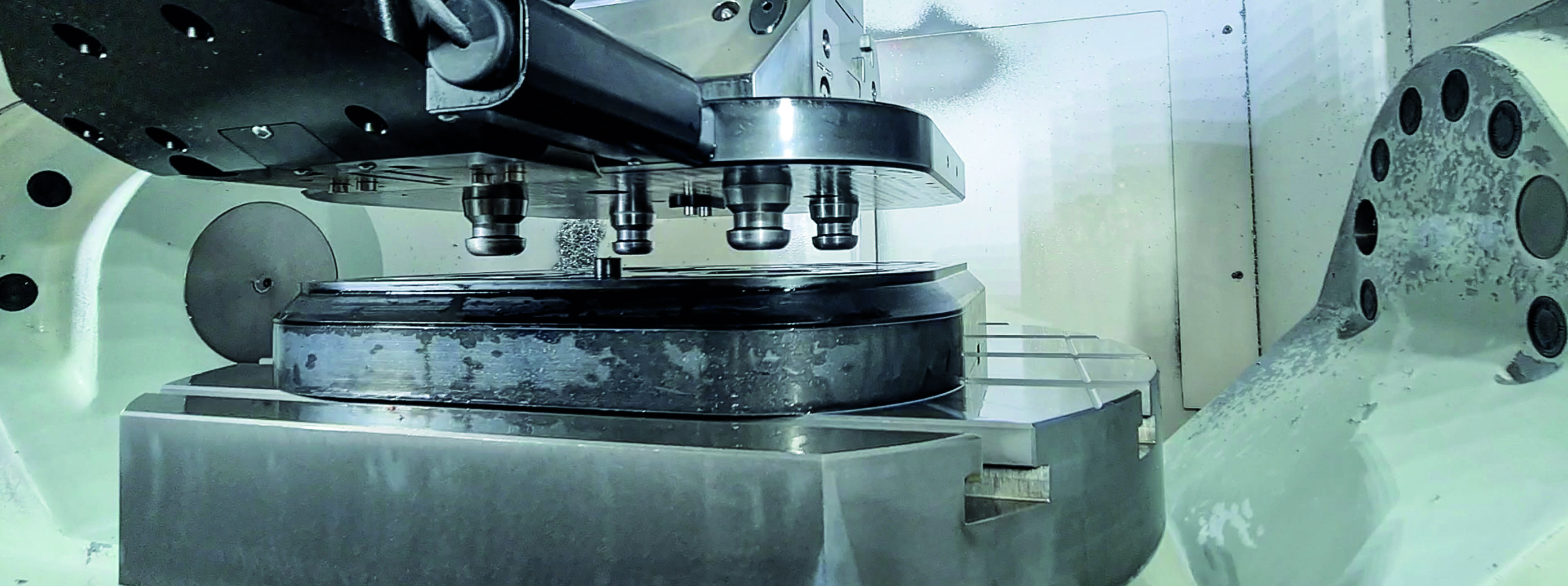
Workpiece loading or pallet loading?
Workpiece loading or pallet loading?
The automation of CNC machines has become a must these days. After all, there is an urgent need for machine capacity, there is a major shortage of technical personnel everywhere and, unfortunately, we still do not appear to be completely free of COVID-19. CNC automation can provide a solution to these and many other challenges we face today. When automating milling machines, we are often asked whether it is best to load and unload workpieces, or rather to load pallets or exchange clamping units.
Detlef Scholz is the Sales Manager at RoboJob in the DACH region (Germany, Austria and Switzerland). He works mainly in southern Germany, but is also active in Switzerland and parts of Austria. "A lot of machining is done in this region, especially milling," says Scholz. "After all, this is where the heart of the German automotive industry is located, as well as precision mechanics and tool mechanics (ed. Hainbuch, Schunk, EWS, Eppinger, Heimatec). Machine manufacturers such as Hermle, Mazak, Hurco and DMG sell hundreds of milling machines here every year to customers who are also in the process of automating."
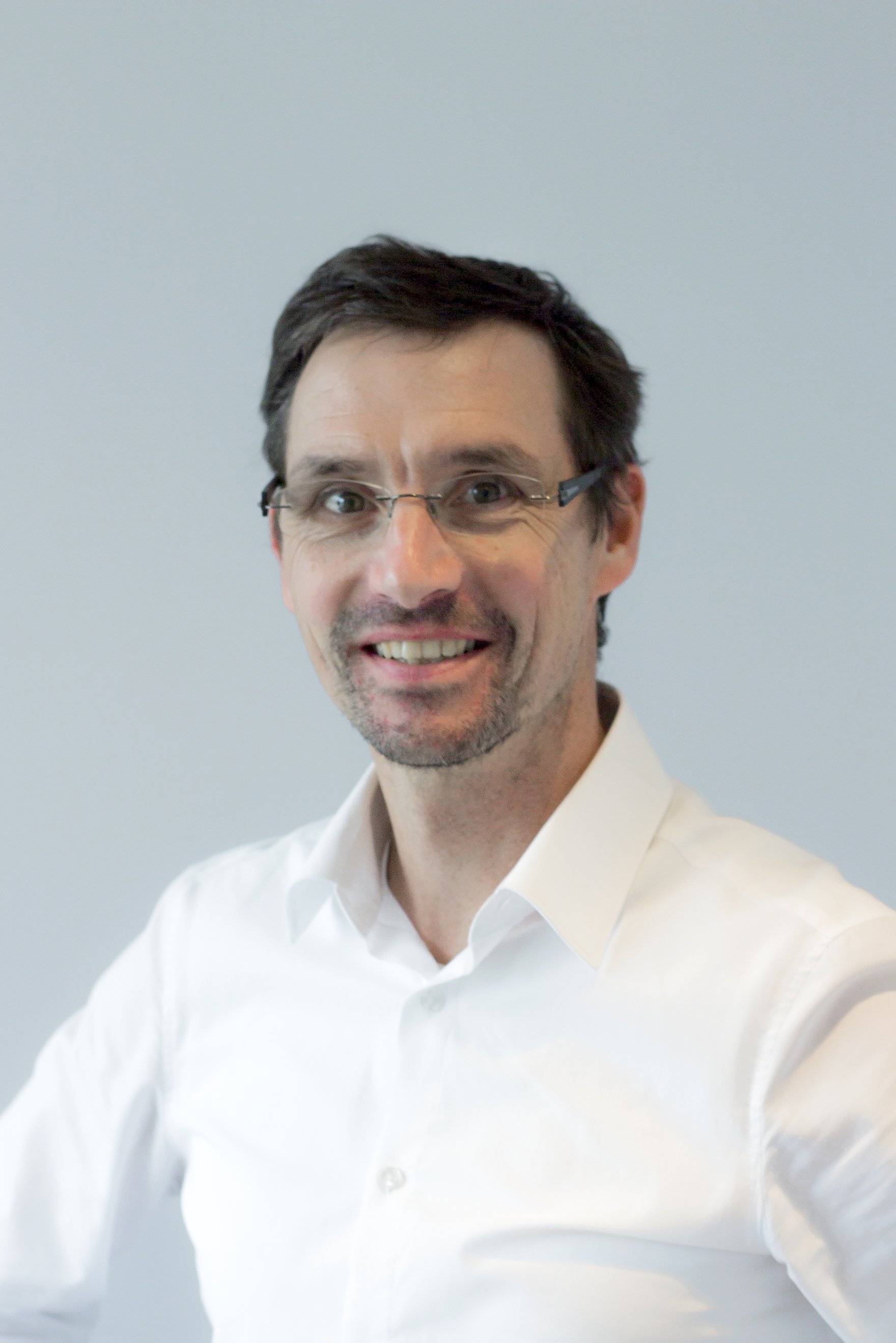
"When I sit down with these companies, I am invariably asked 'What is the best option? Manually clamping multiple pallets and having them loaded by the robot, or having the workpieces loaded individually in the clamping unit in the machine? Many customers have been working in the same way for years and are happy to stick with it," says Scholz. "Companies such as Lang, HWR and Indunorm have established a good foothold here and have won over the customers with their products. It would be difficult to make inroads there. When you want to automate, however, it is important to challenge your current way of working and examine your processes with an open mind."
Many customers have been working in the same way for years and are happy to stick with it.
An operator will often want to manually clamp a workpiece into a pallet and start machining it. After all, this is the way it has always been done: the operator has confidence in this way of working and, at first glance, this is also the most economical way to do it. There are also solutions available, of course, that allow you to clamp two or three workpieces in a single clamping unit. You can also choose from clamping pyramids, a pallet with four workpieces or a clamping bridge with six workpieces. There are even pallet changing systems that can accommodate up to two times twelve workpieces!
That is great and all, but this way of working also has some major disadvantages:
- Time: manually clamping the workpieces in the pallet and also exchanging the workpieces in the pallets takes a lot of time. When you have a shortage of personnel, that becomes a major problem.
- Space: I don't know many customers who don't have a lack of space on the work floor. This way of working also requires extra space.
- Money: every pallet costs money. The more you want to put in, the more expensive it gets. If you think you can work more efficiently with multiple pallets, you will of course spend even more money.
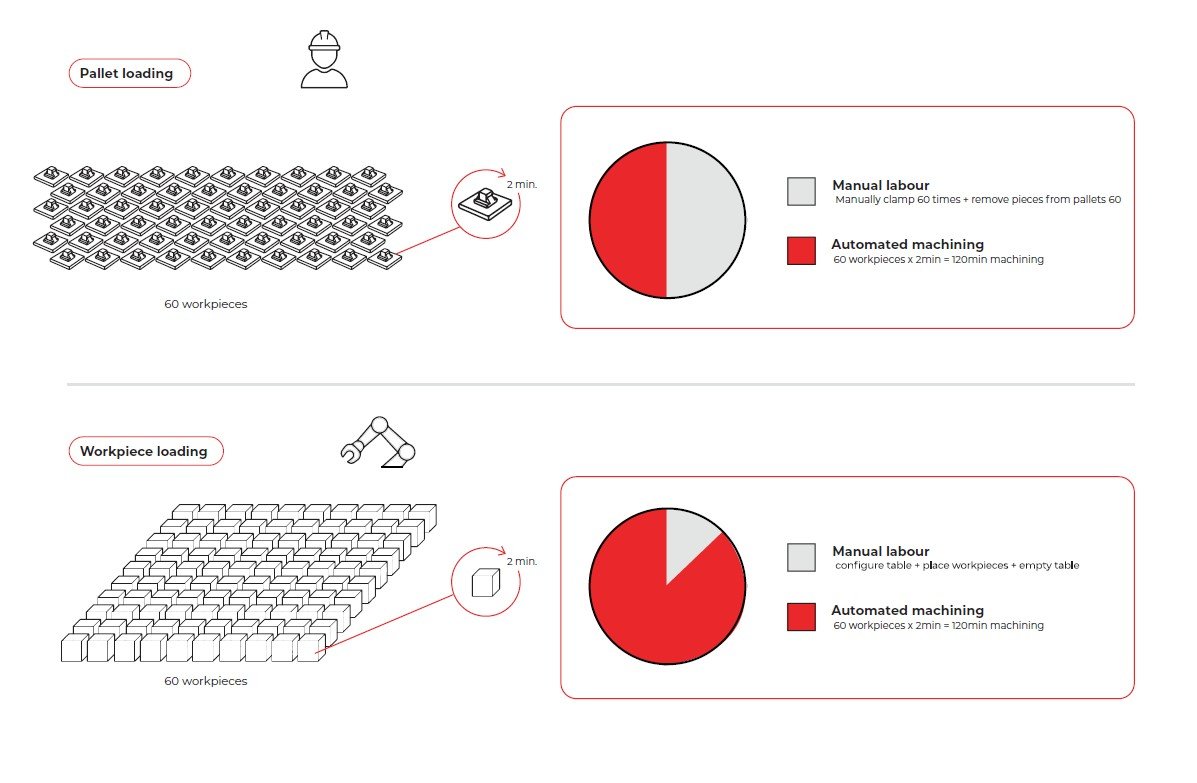
Workpiece loading can be considerably more interesting than pallet loading. Let me give you two concrete examples:
I have a batch of 60 pieces with an individual cycle time of 2 minutes. Suppose I have a warehouse with 60 pallets, I can run my machine autonomously for 120 minutes. First I have to manually clamp 60 times, and after 2 hours I have to take all 60 pieces out of the pallets again. This means that for 2 hours of autonomous machining, at least 1 hour of manual work is required.
If I take the same batch of 60 pieces with an individual cycle time of 2 minutes, but this time I place them on my Mill-Assist, from where they will be loaded into the machine one-by-one by the robot. Configuring the table and placing the workpieces takes me a maximum of 10 minutes, however. Clearing the table could maybe take another 5 minutes. This means that for 2 hours of autonomous machining, I only need to do 15 minutes of manual work. Moreover, I don't need to buy 60 pallets.
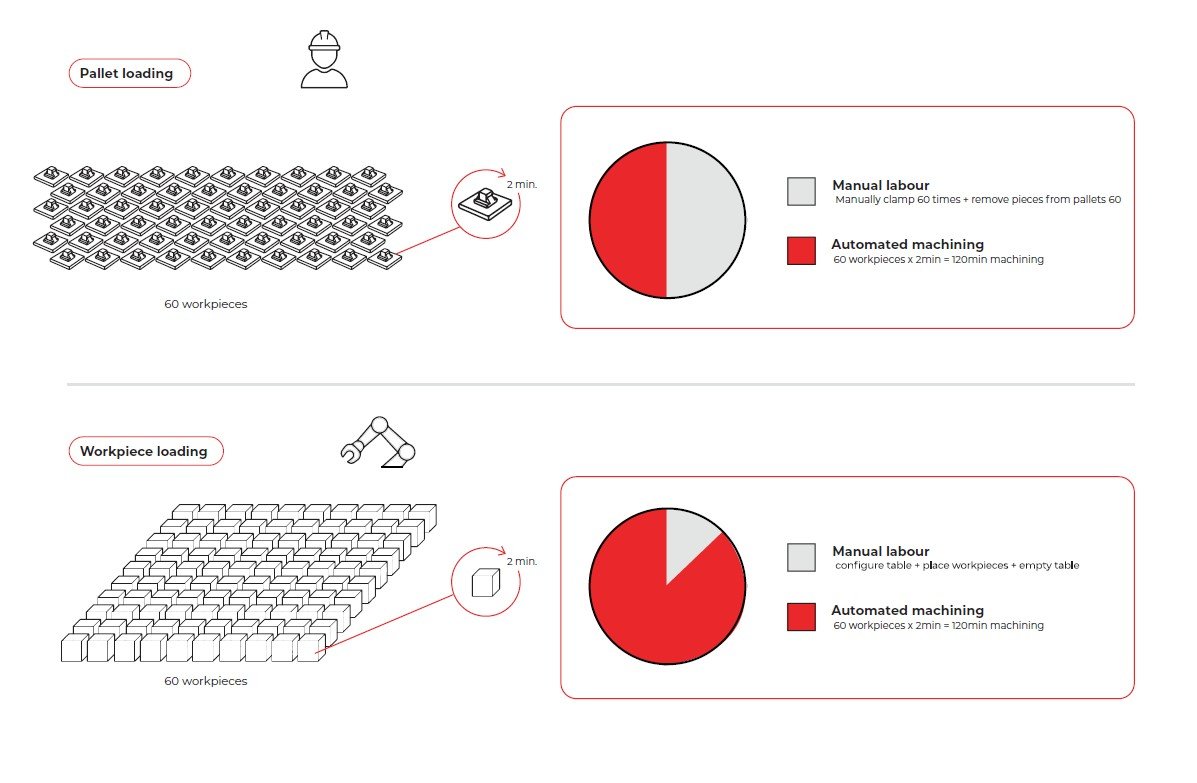
When you want to automate, however, it is important to challenge your current way of working and examine your processes with an open mind.”
"After all, when you want to automate, the idea is to make your production more efficient, right? Taking repetitive, boring work out of the hands of your operator should allow them to be more creative. Well, in my experience, for this type of batch work you should always be able to rely on a robot that loads and unloads the individual workpieces. This improves efficiency, is reliable, faster and cheaper."