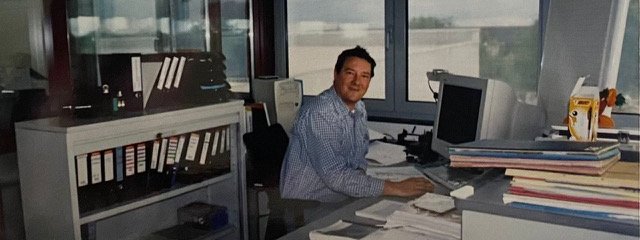
A look ahead with Helmut, CEO RoboJob
A look ahead with Helmut, CEO RoboJob
In our previous conversation, we looked back at RoboJob's past, and how everything once began. We also reflected on RoboJob's milestones and the hurdles we had to overcome to get to where we are today. Today, the world looks very different than it did 20 years ago.
Helmut: "Indeed. Before, it was my neighbor who was the competitor, so to speak: suppliers in Belgium or possibly in neighboring countries. Today we find ourselves in a global market with competitors from all over the world. However, some things are still the same: unfortunately, it is still very difficult to find operators. I would even say that it has become a lot more difficult. Also, the market rates for CNC work are still capped, while labor costs keep rising: in recent years, even with 15% in almost 2 years. Those challenges are the same everywhere in Western Europe and North America.
But let us also dwell on positive trends. Sustainability is one example. The West has realized that we are very dependent on the global economy, and that it is not very wise strategically to transfer technology to low-wage countries. In certain sectors, we see 'Reshoring' in full swing. In the United States, the "Inflation Act" was introduced, and it is acting as a catalyst to bring back certain industries.
I believe that in certain industrialized countries, industry and production will effectively come back: Germany, France, Italy, the Netherlands and hopefully Belgium. These countries are very dependent on industry, especially when you look at their contribution to the GDP. They simply ‘need’ to reshore. And then automation is obviously desperately needed to bridge the wage gap, increase industrial output and as part of a structural solution to cope with an aging population and keep pensions affordable.
Not to mention, thanks to automation and digitalization, we are making our industry attractive again for our employees. We manage to create a much better 'work/life balance'. Personally, I still think this is the most important asset of automation: we now have the opportunity for the first time to stop and reverse the 'race to the bottom'. Thanks to automation and digitalization, we are once again making our companies attractive to young people."
Knowing what you know now: how would you handle things as the person in charge of a machining company or department ?
Helmut: "The answer may not surprise you: invest heavily, in Automation in the first place and also in Digitization. For digitization you need time AND resources, for automation only resources. Once you have taken the step to automation, you will find that it creates time within your company. After all, you take over repetitive tasks from your staff, allowing employees to use the freed up time to work on creative processes, including digitization.
Often a machining company or department is very dependent on a limited number of people within the company. A good turner or an experienced miller are crucial: if you take those people away, you have a problem. Because of the ever-increasing pressure on these people, experienced employees become exhausted. This fantastic profession is no longer attractive to young people, the knowledge of the experienced employees is not or insufficiently passed on, and that is not only harmful for the company, but also regrettable from the point of view of wealth creation.
There are lots of ways today to secure that crucial knowledge within a company: CAD/CAM systems with feature recognition and machining strategies, tool management with proven machining parameters, you name it. That is process digitization within a machining company. The knowledge is secured in a structural way that makes it transferable. However, time must first be created among people to participate in that necessary digitization. Automation makes this possible.
Moreover, low-level automation immediately provides greatly increased billable output per man-hour performed.
I would say: it is no longer a question ‘whether' one should automate and digitize, but 'how'."
Which brings me seamlessly to the next question. There is a very big difference in the offer: in automation there are "entry-level products" like Coby, but also "all-rounders" like a Tower. How do you start as a company without any knowledge of automation?
Helmut: "For companies that are not yet automated, the message is: start simple. You can get to work with a RoboJob Turn- or Mill-Assist, for example, in only a few hours, and it pays for itself in a few months to a maximum of a few years. These products last for at least 15 years. And they also retain their value, making such an investment an absolute no brainer.
When choosing automation, you will need to consider the ease of use for your operators: after all, they are the ones who will have to work with it. Also ask yourself the question: how easy is it for my people to work with automation? If it is too difficult, then automation is not a help but an extra burden. If an automation is really easy to set up, then you should not hesitate.
So easy-to-use automation that pays for itself quickly and does not lose value. If you start with that today, in a few years you will already have more experience and new insights. At that point, you can possibly look at a "high end" automation, which offers more features but is also more complex.
When you automate, you have to get your processes well under control. That's a learning process: so start low-key."
Are the offerings in automation going to change significantly in the future?
Helmut: "What are the physical tasks that can be automated in a machining operation ? These are internal logistics, machine preparation with tools and fixtures, workpiece manipulation, and quality control. With that, I have listed everything that takes place in terms of physical operations. I think that is everything that can be automated. So that's where our focus lies."
Is there any future at all for suppliers without automation?
Helmut: "I honestly think: not in the West. Unless one is just making prototypes, but they too are going to come under increasing pressure from automated companies.
Industry 4.0 refers to the fourth industrial revolution and it is happening right now. After the years when Industry 4.0 was a "buzzword" just like the "Internet of things," you can now see that crystallizing into its final destination: the highly automated work preparation, the highly automated administration but also to where billable hours are created by the highly automated shop floor. That evolution has begun and that is not going to be stopped or reversed.
To make your business structurally flexible, respond with much less stress to the strong fluctuations of a modern Supply Chain, face national and international competition, make your work environment more attractive, and reverse the "race to the bottom," you need to automate now. Not doing it is also a clear choice that costs more money with each day's delay than doing it.
Today we find ourselves in an uncertain market, with inflation still high, high interest rates, unsettled geopolitical conditions, a shrinking economy. Is this really the time to invest in automation?
Helmut: "Absolutely. More than ever even. Personally, I would rather invest in the automation of existing machines than in new machines. After all, that investment pays for itself quickly, and that way you free up resources to renew your machinery or take the next step in automation.
With a shrinking economy, you may have a little too much staff. If you automate now, you can use this period to familiarize your staff with automation. Then, by the end of the recession, you will be ready to shift gears for the next wave of Supply Chain that is coming. So arm yourself now for the future of your business."
You are quietly approaching retirement age. What role will you continue to play at RoboJob?
Helmut: "I am always going to be associated with RoboJob, but rather in an advisory role. My passion is still in product development, and I still get enormous pleasure out of that. I'm going to keep doing that.
But of course I realize that retirement is inevitable eventually. Therefore, I see it as my job to make sure one can do without me in the company. My three sons have all been working at RoboJob for more than 10 years, and they are supported by a good mix of young talent and more experienced employees. The future of RoboJob is in good hands."
Do you still have a goal or dream you want to accomplish at RoboJob before you retire?
Helmut: "We are working on a new concept that I am very keen to finalize. It is a new product that will be presented in a few weeks at the Grand Opening of the new headquarters. I am immensely proud of it, and look forward to presenting it to our customers and partners."