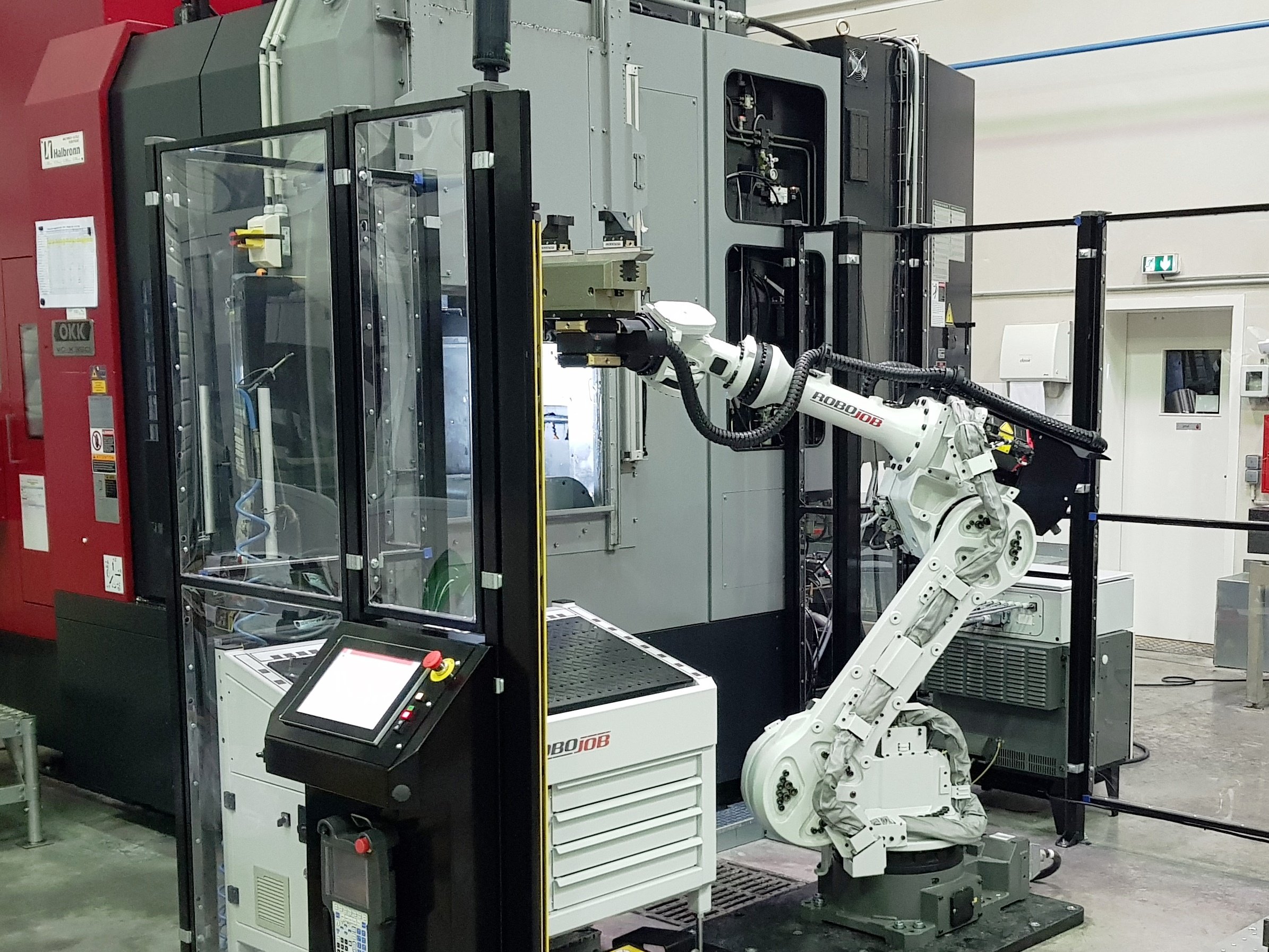
USIDUC
USIDUC
USIDUC
Since 1993, the USIDUC company has developed into a specialist in machining technical parts in a wide range of traditional and advanced materials. With a machine park of 30 CNC machines and 20 qualified operators, the company can manufacture complex parts in small and medium-sized series for industry in materials such as polyamide, polyether ketone, FR4, G11, carbon, titanium, Inconel and Hastelloy. USIDUC is the last producer in France of pre-impregnated pipes.
USIDUC is located in the heart of the Vallée de l’Energie in Franche-Comté and has developed recognized expertise and know-how in the medical, energy and aviation sectors.
In September 2018, RoboJob automated an OKK VCX 350 milling machine in the company using a Mill-Assist Essential, a standard product from RoboJob for automatic loading and unloading. Using a FANUC robot with a payload of 100 kg, it is possible to load a milling machine directly from the Mill-Assist or a pallet, because USIDUC also selected the "PALLET LOAD" option. Thanks to this RoboJob solution, USIDUC is now able to automatically produce small and medium-sized series on its OKK milling machine.
The milling machine that was automated by RoboJob is an OKK VCX 350 machining centre with 5 axes. This type of machine is used relatively often, but USIDUC added a few options, which makes the device a rather unique one of its kind: automated checking of the workpieces in the housing of the machine, a magazine with additional tools for working with sister tools, a specific filtration unit for filtering swarf such as dust emitted by composite materials.
Inès Atmimou, technical-commercial employee at USIDUC: "In the 25 years that USIDUC has been in existence, we have proven that we are an extremely high-quality manufacturer with experience in a wide variety of materials. The only route to such success is continuous investment, not only in infrastructure or machines, but also in automation. Every year, 15% of our turnover is reinvested in new machines, infrastructure and therefore also in automation. In the past year we have invested in 2 milling centres with 5 axes, Robojob automation, 3D printing and more.
We focus on quality. It’s no coincidence that we are both ISO 9001 and ISO EN 9100 certified. The latter is the norm for aviation and places high demands on both the workpiece and the quality and reliability in respect of delivery times. The need for continuity and high quality was our motive for working with Robojob. Moreover, ergonomic working conditions also play a crucial role for our operators.
As a subcontractor, we regularly receive exceptional requests. For example, we manufacture 60 kg workpieces on this milling machine for which the cycle time is six hours. You can imagine that it is certainly not easy for an operator to manually load and unload such items. This however, becomes child's play using automation from RoboJob. We’ve not only succeeded in improving ergonomics in the workplace, but also in increasing the efficiency of the machine. In combination with the Mill-Assist, this machine is able to operate for up to 60 hours at a time.
As for every investment in our machine park, we conducted a thorough market analysis.
We machine different types of materials, such as plastics, composites, ceramics and super alloy type steels. The weight of the parts treated can range from a few tens of grams up to 60 kg and the dimensions vary from a few tens of mm to 25 cm on the sides. The cycle times vary from a few minutes to 5 hours.
Our goal is to run our machining centre 24/24 with an autonomy of 8 hours at night and 48 hours at the weekend. Thanks to the financing spread over 60 months, we hope to achieve an ROI in less than 3 months.
Taking all these requirements into account, we came to the conclusion that RoboJob was the best option for us. The Mill-Assist not only offers high precision and quality, but also great flexibility in order to be able to automate this wide variety of workpieces. The Mill-Assist turned out to be a stable solution and RoboJob a reliable partner.
At USIDUC we are proud of the fact that our production never stops. We work with three shifts per day and with weekend shifts. The company also never closes its doors during the holidays. We produce 24/7, 365 days a year.
This also means that there’s constant pressure to respect delivery times and at the same time to offer high quality.
Taking all this into account, the robots are a welcome help for our operators. And in fact the Mill-Assist fulfils this role exactly: an assistant for our operators in the workplace. They welcomed RoboJob’s automation solution with open arms and are highly enthusiastic about its ease of use."
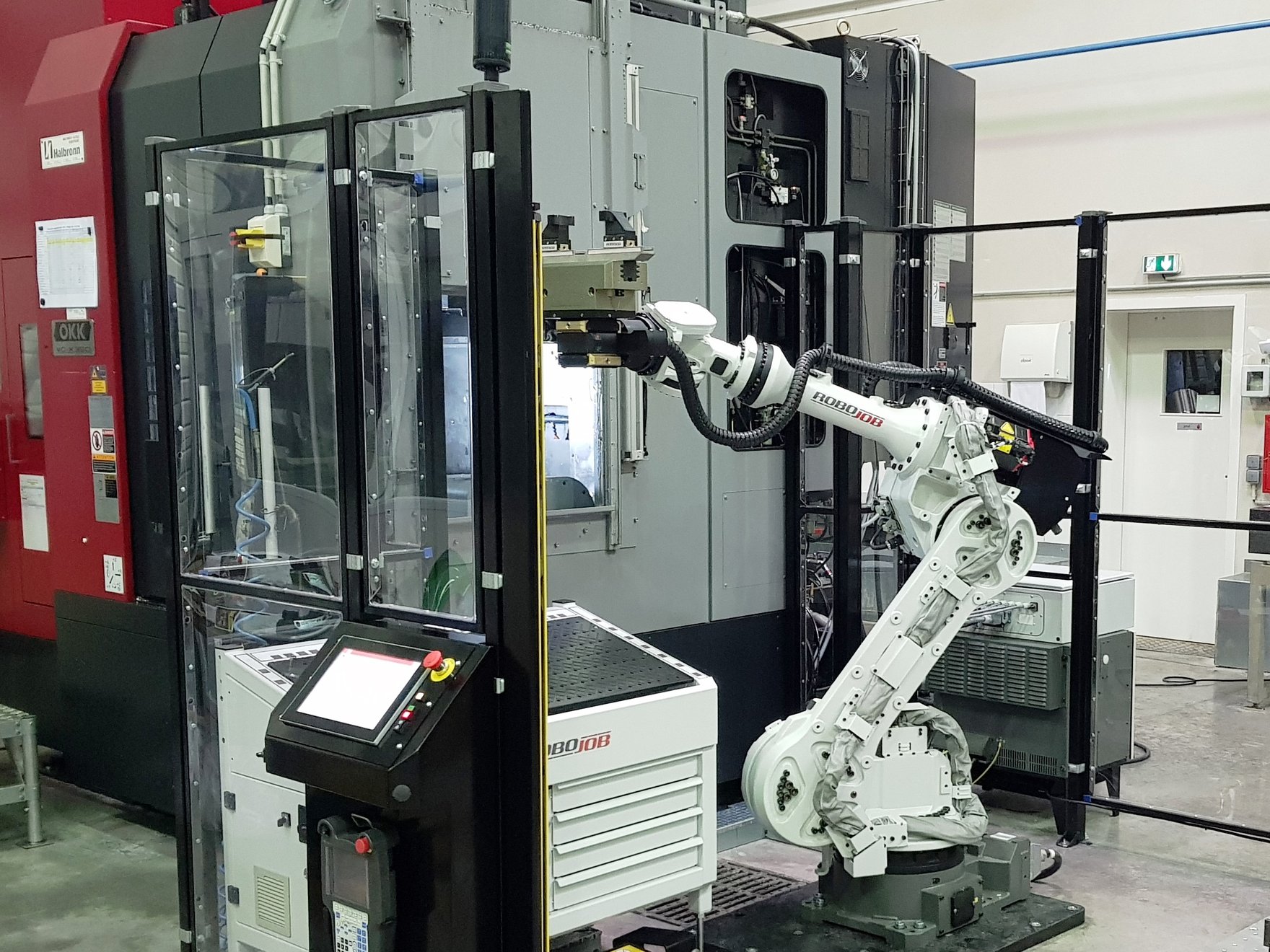