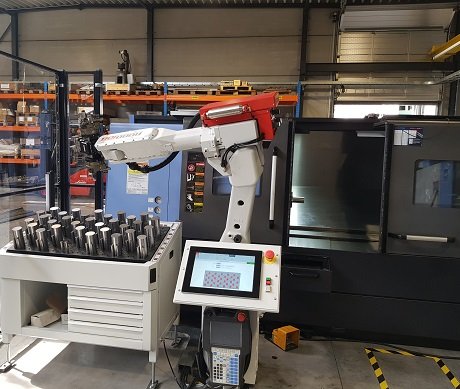
Vanro CNC
Vanro CNC
Vanro CNC is a fairly young Belgian supplier of turning and milling work. The company was founded in 2006 by Rony Vanwynsberghe, then still in a secondary occupation. It soon became clear that this was Rony's passion, and before the end of that same year he decided to go all out. The results would not be long in coming. Rony set up a one-man business and found a larger building where he could further expand his business. A building of its own was purchased in 2012. Barely 10 years after the start of the company, this was a huge milestone. But the growth story of Vanro CNC doesn’t stop there.
Rony Vanwynsberghe, Business Manager “Today we have a team of 7 people. They keep 5 turning machines and 4 milling machines running. This of course is only possible because individually they are all driven, capable people. But it’s also because we focus on automation. It has become very difficult to find good operators. Furthermore, the wage costs are considerable and the hourly costs of these people are quite expensive. So it goes without saying that I prefer not to use my people for repetitive work. We prefer to automate the repetition work so that we can deploy our people for other tasks. We must be able to use them efficiently for piece work as well as urgent repairs; those tasks where they really add value to the company. Moreover, they prefer to do those kinds of tasks rather than just putting pieces in and out of the machine.
That’s also the reason why we’ve already purchased a second automation system. The first already arrived in 2017: using our first robot we’re able to automate both a Brother milling machine and a Mazak lathe. We’re able to move this robot from one machine to another. It’s just a matter of unscrewing 6 bolts and you can then move the whole thing and plug it into the other machine. However, in practice we don't do that very often: it makes more sense to ensure that you have enough work for one machine and then let the robot work on it as much as possible.
We purchased our second robot in 2019: a Turn-Assist Essential that we had installed on a Doosan Puma GT3100LM. Just like our Brother and Mazak, this was also an existing machine. The interesting thing about our second purchase is that we’re able to use all the tooling that we already had for our first robot on this second robot. That again saves us costs. We mainly produce larger pieces on the Doosan.
When I now look back on both installations, I’m highly satisfied with the entire process. I also notice that RoboJob is taking further steps as an organisation and that the entire support is improving even further. I am also very satisfied with the Service. Even on Saturdays I can call them and immediately receive further assistance. And most importantly in the whole story: both RoboJob systems are extremely reliable. It's just a matter of pressing the button and those robots start working. Every time!”
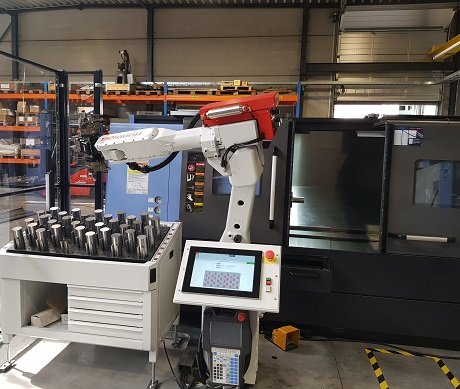