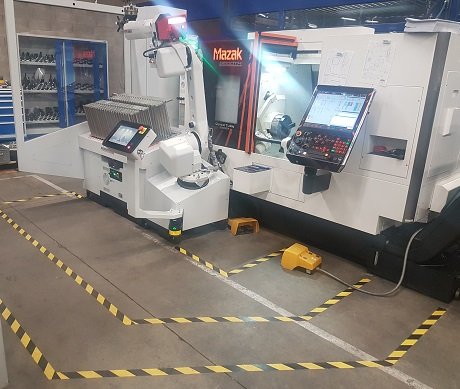
URMA SARL
URMA SARL
Founded in 1985, URMA SARL specialises in the following fields: precision mechanics, milling, turning, as well as fitting and assembly of mechanical components.
URMA SARL is for its customers the preferred partner for services of an industrial company capable of producing their assemblies: from the manufacture and assembly of parts to the delivery of finished products.
The URMA company is positioned as an ideal partner for a large, varied clientele, mainly active in sectors such as the automotive and petrochemical industry.
Joris Bisschoff: "URMA SARL is a subcontractor par excellence. We manufacture a range of very diverse mechanical parts. While we produced relatively large series in the past, the size of the latter has decreased significantly over the years. Today we mainly produce small series, a job that is rarely interesting for our operators, so to make their life a bit more pleasant, we decided to take a closer look at the possibilities of automation. An undeniable advantage: the uninterrupted continuation of production in the evening, at night or at the weekend, even when there’s no operator present, inevitably leads to a significant improvement in the efficiency and output of the machines.
We came into contact with RoboJob at a trade fair. After seeing one of their systems at work on a Mazak Integrex, we spoke with Jan Van de Wouwer, regional sales director at RoboJob, who gave us a demonstration of the system and its control software. The simplicity and user-friendliness of this intuitive system catches the eye. We have been working with Mazak machines for years and their software is based on the same philosophy: it has to be both simple and intuitive. The fact that a multinational such as Mazak works with RoboJob has given us a lot of confidence in this company.
Ultimately, we decided to automate our Mazak Quick Turn 250 MSY with a RoboJob Turn-Assist 270 i. Installed in January 2019, this automation solution is a real pleasure. It took just four days to install the system and get our robot up and running. In addition to the flawless installation and commissioning process, we’ve only had to call customer service once in connection with a software query, which was answered immediately. Apart from this one-time assistance, we’ve been able to work with our robot continuously without any problems.
The implementation of our robot has led to a significant improvement in the continuity of our production. After all, a robot does not need breaks. We use it two or three times a day for small batches. Because setting up and adjusting our robot only takes a few minutes, it’s almost immediately put back into operation. The operator can then perform other tasks. Consequently, the much faster execution of our small batches has had a positive effect on our profit.
We’ve also used our robot during the lockdown. Despite the absence of operators, our robot enabled us to produce a number of batches."
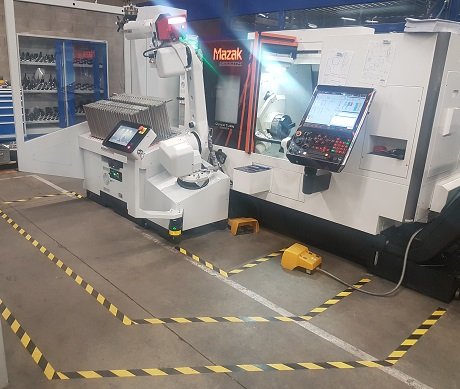