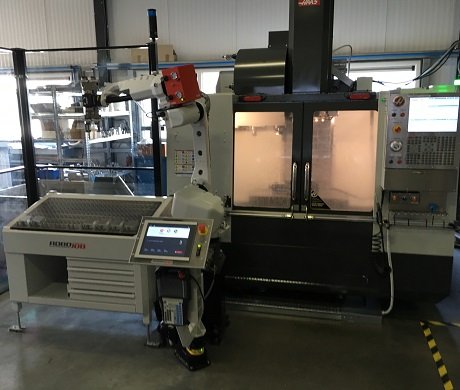
Paricla Fijnmechanische Techniek
Paricla Fijnmechanische Techniek
Paricla Fijnmechanische Techniek
The 2 owners, Wolter and Tinie van den Broek, set up Fijnmechanische Techniek from scratch in 1998. Time was already taken to develop a vision and strategy for the company two years before the actual start. This vision - in which continuous improvement, innovation and investment are the basic principles - remains the key to the success of Paricla today.
At the start they produced using conventional machines, but soon the step was taken towards computer-controlled machines. The machine park was systematically expanded, and in 2009 the company moved to new premises in Stadskanaal. In the meantime the company now has numerous CNC machines and has six employees.
Paricla thinks ahead. In recent years the company has invested heavily in automation, so that it can offer better delivery times, also for larger batches, and always with extremely high quality components.
Wolter and Tinie van den Broek, Owners: “Just under two years ago, the two of us decided to automate, and there is a very simple reason for that: you just have to take that route if you want to retain a market share in the Netherlands. This has to do with spindle hours and efficiency: without automation we attain 5.5 to a maximum of 6 hours per day. In order to remain competitive, we have to increase the spindle hours and efficiency. It is also very difficult to find good workers in the Netherlands. We notice that schools don’t always manage to teach the necessary knowledge so that young school leavers quickly find their way to and into our sector. With Paricla we’re doing everything possible to change that, by offering talented students with an affinity for metal an internship. But it’s not easy to achieve.
These two factors made us think about automation: what do we want to automate, and how do we want to tackle that? We thought about this very openly, together with our employees.
Our employees have already been with us for several years and it was they who put the question as to whether a robot would take work from them. That was obviously not the intention: rather, we wanted to change our way of working. Indeed we were always running behind the facts because we didn’t have our process completely under control.
Our quest started online and we then went to the Techni-Show. We met up with the various providers in the market, and sat round the table with them. We had a very good feeling with RoboJob right from the start. We went to their showroom in Heist-op-den-Berg, and there we could also see from which machining company RoboJob itself originated. We gained a far better understanding of the way they work at RoboJob, and of course their automation itself. In doing so we became convinced of the significant ease of use of the Mill-Assist Essential. It is so simple and user-friendly.
What we didn’t want was 1 robot between 2 machines. If we did that we’d have to make concessions on flexibility. We wanted 1 robot on 1 machine, so that we could still keep 2 machines free, which we wanted keep deploying flexibly.
Four months ago our Mill-Assist Essential was installed on a Haas VF 2 milling machine. Thanks to RoboJob’s good contacts with Haas, the installation went perfectly. And now we’re already able to reap the benefits of our process automation: using RoboJob automation we are now at a whopping 16 spindle hours a day. We now engage our robot also at night and during the weekend. Last night, the Mill-Assist continued working and this morning there were 96 products ready. It turns out to be a very simple solution to increase our spindle hours.
We are extremely satisfied with our collaboration with RoboJob. We’ve been able to increase our spindle hours with very user-friendly automation. The installation went flawlessly thanks to their excellent contacts with Haas. Plus we’ve shown that thanks to automation, we’re not scrapping any jobs, but creating new jobs. At the time we bought our robot, we had 4 employees. Now we have 6. Resources have now been freed up so that we can invest further in our capacity and in our machines. For these reasons, we are going to increase our production hall in order to expand our production processes so that we can automate further with a view to the future."
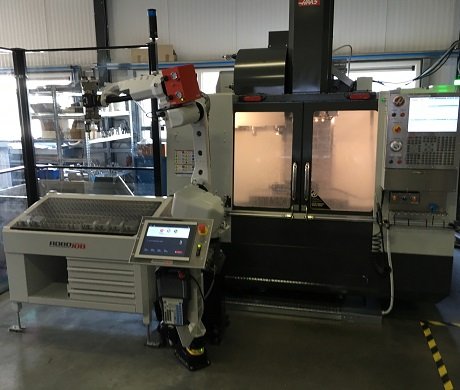