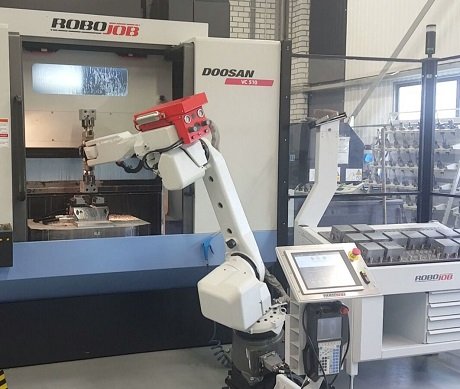
Mabotec BV
MABOTEC BV - short for Manifold Boortechniek -
is an established name in the world of 'hydraulic manifolds’.
Mabotec BV
MABOTEC BV - short for Manifold Boortechniek - is an established name in the world of 'hydraulic manifolds’.
MABOTEC BV - short for Manifold Boortechniek - is an established name in the world of 'hydraulic manifolds’. For 20 years now, the supplier has been producing hydraulic control blocks in single pieces, and occasionally in small to large series. For that it has many CNC machines, which it also uses for unmanned production. This way, a number of machines can continue to run at night and as a consequence they do not work in a shift system.
MABOTEC differentiates itself by focusing on quality and efficiency. Not only with automation but also with the ISO 9001 certificate, whereby the highly experienced machine operators are accustomed to working in accordance with ISO 9001 standards. Apart from that, Mabotec is also a recognized training company. They regularly train young people to become skilled workers and this way the company ensures itself with highly skilled operators of the future.
We think ahead at MABOTEC: it shows in our modern machine park, our ISO certification and also through our Tool Management System from Zoller, which is linked to our CAD / CAM software. This way we try to pursue the highest possible quality and efficiency, and at the same time to position ourselves as an attractive employer.
Mabotec employs 30 people and there is little turnover of labour. The flip side of the coin is that our employees are getting older and so we need to find a new influx of young people. That's why we train young talents and we endeavour to promote our industry to them. That is only possible by an employer also focusing on innovation at every level, and hence automation.
At Mabotec we’re not really specialised in serial work but more particularly on single pieces. And yet we wanted to automate. In order to increase efficiency, to improve our output and to show our young employees - several of whom are still at school - the robotics process and make it tangible. And so we went looking for a low- threshold system, which we wanted in order to automate the entire small series even from 5 pieces.
We got to know RoboJob some 4 odd years ago at the Open House of a machine supplier. Since then, we heard from them regularly, but of course we also were on the lookout for other solutions. Eventually we deliberately opted for product handling, because that seemed to be the easiest solution for our products.
RoboJob were able to offer us the simplest solution in the market with the Mill-Assist Essential. With this automation, we have a low-threshold system with very easy controls. In March 2016, we had our robot installed on an existing, 3-axis Doosan VC 510.
This machine did not have a robot interface but RoboJob took over the reins and directly coordinated the matter with Dormac, our machine supplier. So we only needed to watch from the side-lines that everything was done.
And no sooner said than done: RoboJob came to measure up everything beforehand and the installation itself was completed in a few days. After that our operators were also trained on the spot, using our own workpieces. And then we could immediately set to work.
Looking back, the move to automation was a good decision. For us it has been a good investment, and we’re continuing to look closely into how we can get even more out of it.
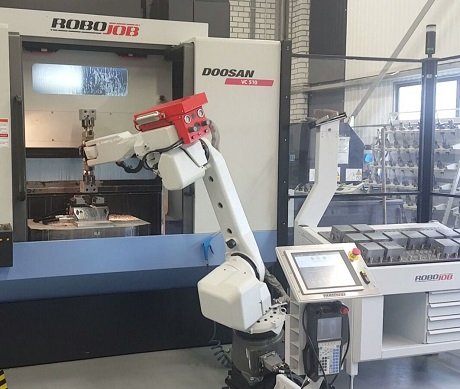