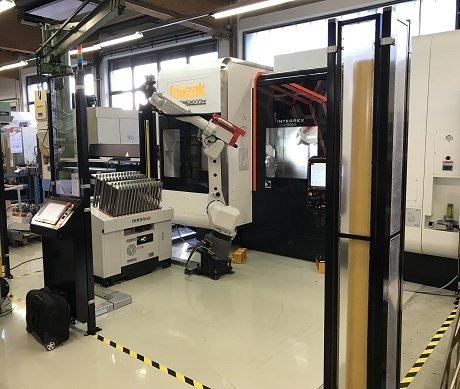
HEB Hydraulik-Elementebau GmbH
HEB Hydraulik-Elementebau GmbH
HEB Hydraulik-Elementebau GmbH in Freiburg is one of the leading manufacturers of high-quality hydraulic cylinders that are used worldwide in a wide variety of industries. Over the past 40 years, the company has developed into one of the leading hydraulic cylinder manufacturers with an extensive range of products and services. The family business employs 70 people and has representatives all over the world. The Freiburg site develops and produces high-quality round and block cylinders, flange and screw cylinders, standard and road measuring cylinders, locking and multi-position cylinders and highly specialised special constructions. Intelligent technologies, state-of-the-art CNC technology and powerful automation enable maximum flexibility and efficiency, both in the design and in the rapid delivery of the cylinder. The best materials and compliance with demanding HEB standards characterise all our products.
Philipp Hamann, K-Team management: “In these times it is of course always important to focus on efficiency, capacity and flexibility. That’s also the case in our company. Our goal was to reduce 'down time' in our production by implementing automation. We wanted to get more spindle hours out of our machines without having to hire more people.
Another objective was to let our operators focus on their main task: preparing the machines for the next job. We found that this was often difficult because they had to combine physical, repetitive tasks with creative tasks. We wanted to improve our efficiency, creativity, capacity and flexibility through the implementation of automation.
So we talked to our machine suppliers and RoboJob was immediately mentioned. A number of our machine suppliers had already worked with them and one of our colleagues had also met RoboJob. So I looked them up on the Internet and contacted Mr. De Roovere. We arranged a meeting with him and he introduced us to RoboJob's products.
We were highly impressed with RoboJob‘s software: RoboJob really makes the difference here. We also compared the offer with that of other suppliers, but no one could offer the same level of user-friendliness. It is so easy to operate plus it’s also logical and modular in design. Anyone could work with the platform.
Our first RoboJob system was installed in November 2018 and we automated our Mazak Integrex I200 with a Turn-Assist 200 i. The entire preparation and installation went smoothly and we were able to use this system immediately. Notwithstanding the fact that this an extremely compact automation system, we have mainly used it for our larger batches. The results and also the feedback from our operators were very positive, which made us think of a second robot. Just 8 months after the first robot, a second Turn-Assist 200 i was installed, this time on a DMG CLX 350V6. This machine is mainly used for smaller batches. This second installation was a bit more demanding because we don't have much room on this machine. However, RoboJob was flexible enough to provide us with an excellent solution for minimising floor space.
Both systems function smoothly. We have increased both our capacity and our flexibility. It is easy to switch from one product to another and this has also resulted in less stress for our operators. In the past they were under significant pressure to keep up with our schedule. We’re now seeing that it’s become a lot easier for them to follow that schedule. They’re now able to operate multiple machines and we’ve significantly increased our spindle hours. I am not only satisfied with the RoboJob systems, but also with RoboJob as an organisation and supplier. There was a small language barrier at times, but that’s now improved since RoboJob founded the technology centre in Germany. We’re currently considering a third automation solution. I’m already looking forward to our next project with RoboJob.”
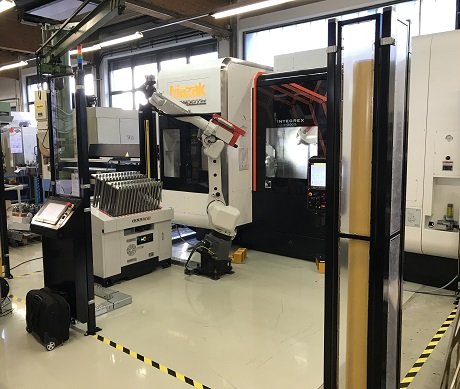