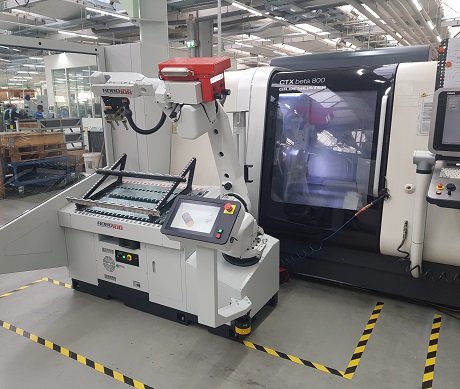
Gerhard Schubert GmbH
Gerhard Schubert GmbH
Gerhard Schubert GmbH
Unerringly and always looking forward, Schubert Packaging machines focuses on the current and future needs of its customers. With its philosophy of modular and intelligent TLM packaging systems, the company is boldly steering a completely autonomous technological course. The aim is to offer future-proof solutions to the customer, which are easy to operate, flexible in size conversion and extremely efficient as well as stable in function. The company regularly introduces major leaps in innovation that offer the customer benefits in new dimensions, and also wins new market segments with new technologies.
The business group was established about 50 years ago, the second generation of which currently has 1,100 employees on the payroll. Based on mutual trust and high personal responsibility, the company has succeeded in developing its entirely own innovation culture. In addition to international branches, the Schubert group includes subsidiaries in the IT, Engineering, Precision Components and Packaging Service sectors.
The parts of the TLM packaging machines are made in components manufacturing and at 35 supplier companies around Crailsheim.
Gerhard Schubert GmbH building industry is also constructing proprietary automation, including robots with two, three and four axes. These robots have their own control and scanner. Everything is developed and constructed in Crailsheim and installed from various service centres worldwide.
Marcus Schindler, Components Manufacturing Manager: „It goes without saying that automation is part of our DNA. We construct our proprietary automation for our branch, which is why we also set such high demands on the automation of our machines.
Automation enables us to utilize our machine capacities more efficiently and to produce more overnight. This way we’re able to produce with the flexibility needed in a two shift system during the day and manufacture the series at night using the automation.
I met up with another RoboJob customer through a contact, who was extremely enthusiastic about his own RoboJob automation. That motivated us to contact RoboJob. After three meetings, it was already clear to us that this was an opportune solution and also a suitable supplier for us.
In October 2016 our DMG CTX800TC was automated with the Turn-Assist 250.
3 days were initially scheduled for installation and training, but after 2 days everything had already been completed. During the training, three standard components were programmed with our employees. Our goal with this automation was to produce for 5 hours at night with this machine. This goal was already achieved during the first night.
We now use our Turn-Assist to automatically produce six of our standard products at night. When it needs to be done using RoboJob, we don’t need to worry. With RoboJob, we have now only taken the first step in automating our machines. This has convinced us that we are able to take many new steps in the field of automation.
RoboJob is a young, but highly professional enterprise. It's really nice working together with them, both on a business and on an operational level. My colleagues were also thoroughly impressed with the installation. Unfortunately we rarely come across a team that works as professionally and punctually as that of RoboJob. Hats off to them!”
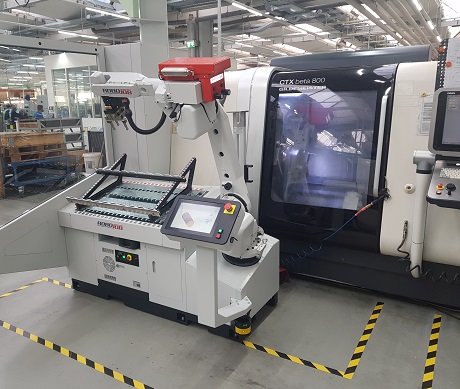