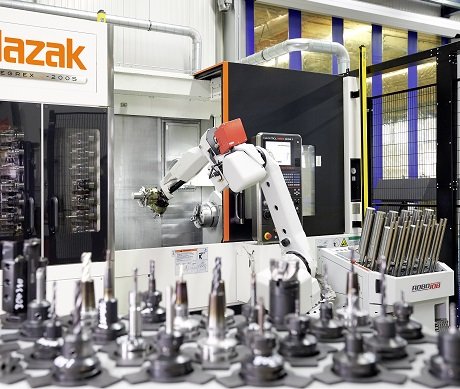
Franz H. Bruder GmbH
Franz H. Bruder GmbH
As a supplier in a wide range of industries, Franz H. Bruder GmbH and its 90 employees successfully completes more than 6,000 orders a year. In the past 40 years, the medium-sized family business has been able to gain extremely broad experience and knowledge in the production of complex precision components. Since 2017, this supplier has once again been investing considerably in the machinery: not only machines for turning, milling and grinding have been replaced or renewed. Automation has also been introduced at this supplier. This means that Franz H. Bruder GmbH is able to continue ensuring its customers of its ability to produce competitively priced and timely-delivered precision components in the future.
Kornel Bruder, Business Manager: "We’ve been extraordinarily busy in the workplace in recent years, having received many high-volume orders from our customers. In our machine park we work in a cell with 3 Mazak Integrex machines, among other machines. We have tried to keep that cell working continuously in 2 shifts, each with 2 operators. However, we came to the conclusion that that wasn’t possible without a third operator, or without automation. We then started to delve into the range of automation, and got to know RoboJob at a trade show.
My understanding of automation was always that it was something for large industries, such as the automobile industry. For a medium-sized supplier with small series, this seemed impossible to me. But then I got to know RoboJob. They made me realize that automation isn’t only possible for us, but also relevant. RoboJob can already demonstrate a great deal of experience, also with the automation of existing Mazak machines. That convinced me to choose them.
Our Integrex J-200 is not, as it happens, a new machine and therefore had no automatic door nor robot interface. Nevertheless, RoboJob succeeded in automating this machine in less than a week. And I’m also talking about the automation of the door, the robot interface and half a day’s training for our operators. That blew my socks off!
We’re now able to keep the 3 Integrex machines working continuously in 2 shifts, each with 2 operators. Moreover, with the RoboJob Turn-Assist on the Integrex, we’re able to run a third shift, manfree. In this way we’ve managed to take away routine work from our operators. They’re now able to focus on high-demanding tasks such as programming, work preparation and processes. They’ve received more help by using the Turn-Assist, and experience this also as an opportunity to work with new technology. As a company, we’ve now succeeded in significantly increasing our capacity and productivity and without having to hire extra people for this.
Our robot has been running very stably for almost 3 years now. A few months after the installation, we received a software update, which caused some hiccups, but that too was quickly resolved. Since then everything’s been running perfectly.
I’ve now also realized that you don’t necessarily have to invest in large automation systems or large machines. We now have the smallest possible automation system, but for us this is already making a world of difference. In past years it was so busy, with so much work, that I can't imagine how we could have achieved that without a robot. Our new vision is that we don’t necessarily have to invest in more machines or more people, but in automation: thanks to automation, the same machines and staff can effectively increase machine uptime and thereby dramatically increase productivity. In my eyes there are only benefits, also for the people who work with it.”
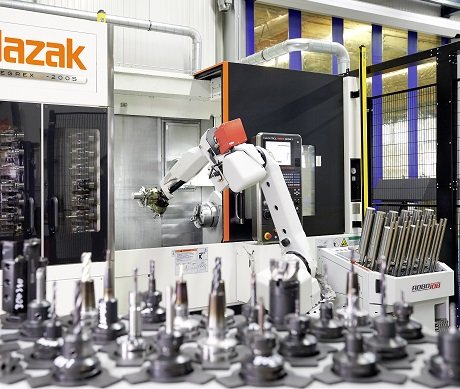