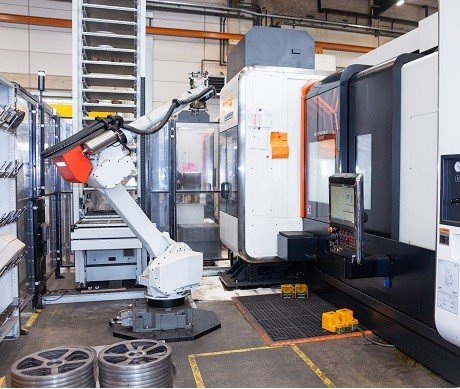
Fecken-Kirfel GmbH & Co. KG
Fecken-Kirfel GmbH & Co. KG
Fecken-Kirfel GmbH & Co. KG
Founded in 1870, Fecken-Kirfel GmbH & Co.KG, Aachen / Germany has been developing and producing high-quality cutting machines since the 1950s for use in very specific areas: they are used to process flexible foam, solid plastics such as rubber and neoprene, rigid foam and cork, as well as other special materials. These materials are used in the mattress and furniture industry, packaging industry, automotive industry, construction, sports and leisure, aviation and medical technology. Fecken-Kirfel is a technology and innovation leader in the cutting machines sector. The Fecken-Kirfel philosophy is to take the lead in terms of technology, quality and service, in line with its motto: Tradition – Innovation – Future.
In line with this philosophy, Fecken-Kirfel has continued to run development and production in Aachen, with an in-house production ratio of more than 90%. Fecken-Kirfel has consistently automated production since the mid-1980s, focusing in particular on high-quality machines and systems that are incredibly reliable, productive and flexible and that also allow unmanned processing overnight and at weekends. Production mainly uses high-quality CNC machines with appropriate automation.
In 2016 und 2017, the company looked at ways to improve the production of small components, which had been made on two CNC turning machines and a CNC milling cell until then. As with any investment, considerations included the state of the art, future development opportunities, possible increases in productivity and safeguarding production capability through redundancy. The new machines and systems also needed to demonstrate a high level of flexibility in order for even the smallest batch sizes to be produced economically while ensuring high quality. Further criteria included the finished/complete processing of workpieces and the reduction of set-up times. The automation solution needed to ensure higher productivity, particularly given that there were increasingly fewer qualified employees to be found in the labour market.
Detailed market research indicated that the best choice for component production would be turning and milling centres with a corresponding automation solution. After corresponding market analysis and an evaluation of the various providers and solutions, the Mazak Integrex i200 s turning and milling centre was chosen, combined with an automation solution from RoboJob.
Managing Director Norbert Leyens describes the strategy worked out with Head of Production Markus Frings as follows:
Our search for a reliable, high-quality multi-tasking machine with an automation solution was essential for our production. Alongside quality and precision, the decisive factors were also the organisation and reliability of the suppliers and their guidance as we converted and reorganised production. The joint solution offered by Mazak and RoboJob convinced us, particularly because of their proven high-performing partnership based on numerous joint projects. It was also significant that the relationship between the two high-tech companies had existed for years and that Mazak and RoboJob knew each other well. This is vital, given that the automation solution needs to work smoothly together with the processing machine.
Our aim was to set up automation in our production that was entirely flexible and that ensured safe, precise workpiece handling. This also means adaptations on the workpiece are needed in terms of dimensions, required gripping force and correct positioning.
Along with all the technical aspects and their cooperation with Mazak, we chose RoboJob because its Tower automation system is revolutionary, high-performing and flexible and fully meets our expectations and requirements. We were so convinced by the concept that we were one of the first customers to order the new Tower.
Due to the development time of the first Tower, the first Mazak Integrex i200 s was supplied with Turn-Assist 250 automation from RoboJob. A year later, a second – identical – Mazak Integrex i200 s with RoboJob Tower automation was installed.
Markus Frings compares the two automation solutions:
With the two systems in place, we are in a unique position to be able to compare both automation solutions. We were able to implement unmanned production with the Turn-Assist immediately after installation. This automation is accessible and easy to use. It increased productivity significantly right from the start. It was a little trickier to commission the Tower: this automation offers a lot more functionality, capacity and flexibility, which places higher demands on the operators, meaning a longer learning curve.
However, when you compare the increase in productivity of the Turn-Assist with that of the Tower, the difference is significant. The Tower has far more storage capacity and a lot of additional technical options: the ability to exchange clamping devices, more flexibility because you can change to producing very different workpieces, even in small quantities. Another major advantage that the Tower has over the Turn Assist is that you can load and unload it without interrupting the production process. The robot continues working on the machine side while the operator removes the finished workpieces on the other side of the Tower and inserts new blanks.
Meanwhile, RoboJob has been working intensively on developing the gripper and the second generation of the RoboJob servo gripper is now available.
Norbert Leyens:
We have now practically reached our objective, because the new RoboJob servo gripper significantly increases the flexibility of the Tower. Fecken-Kirfel will therefore equip its existing Tower automation with the new servo grippers this year. We will also replace the Turn-Assist automation with a second Tower with servo gripper.
We can only make optimum use of the options for finished and complete processing offered by Mazak Integrex when we have a corresponding automation solution. The RoboJob Tower automation exemplifies this and is absolutely convincing, particularly with the servo grippers that are now available. However, we mustn't forget that using them places higher demands on our production planning. In fact, alongside actual work on the machines, our planning and scheduling tasks have become even more important in this regard. Here at Fecken-Kirfel, we are convinced that the Tower automation will help us take our production to the next level.
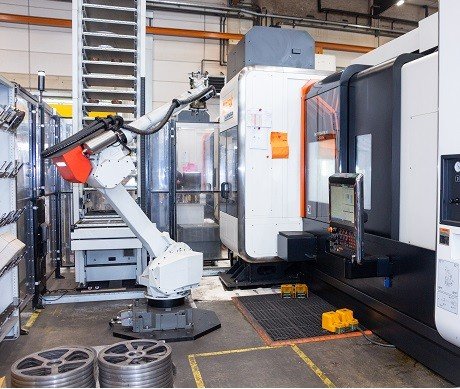