
Ets. Joskin S.A.
Between the green hills of the Pays de Herve lies a Belgian industrial gem: the JOSKIN company.
Ets. Joskin S.A.
Between the green hills of the Pays de Herve lies a Belgian industrial gem: the JOSKIN company. Since its establishment in 1968, this company has been manufacturing the world's largest range of materials for the distribution and transport of agricultural products. Their machines traverse the countryside of Europe and many regions of the world. Almost 60 countries are supplied regularly every year.
In order to achieve this, JOSKIN relies on its 820 employees in no fewer than 5 production sites: Belgium (2), France (2) and Poland (1). Among these is a branch in Soumagne with a total area of 15.80 ha. This is the heart of their production with modern CNC machines. What’s more, 3 Turn-Assists from Robojob were added at the end of 2018.
Didier Schildwachter, head of the Machining department: “Although we’re an important employer in the region, the search for skilled workers is becoming increasingly difficult. That’s why we’ve fully focused on automation. We met Robojob for the first time at the TechniShow in 2013 and we were highly impressed with their concept. Robojob has many years of experience in automation and can boast more than 25 years of experience in the machining industry. We also noticed that they fully focus on quality and simplicity. You can see this not only in the quality of their products and suppliers, but also in the care with which they program. This means that the Turn-Assist is very easy to operate and that the programming and change times are very short. As a result, production is more profitable, even for small series. All these elements turned out to be crucial reasons for choosing Robojob.
By using automation, we aim to achieve a higher return than with manual loading. We’ve not only achieved this goal, but we’ve also achieved a higher production capacity.
We bought 3 systems from Robojob and the first 2 robots were already installed with 1 week. The training went just as quickly thanks to the user-friendliness of the system. The third installation was a bit more difficult and took a little more time considering the size of the robot and the parts to be handled, but everything went smoothly.
Using these 3 systems we’re producing more than 4,000 pieces per month. These numbers speak for themselves and we’re convinced that we can do even better! We operate with 2 shifts, 5 days a week. Because we believe 100% in the work Robojob delivered, we load them to the maximum in the evening so that they can operate unmanned at night. Depending on the pieces, the working time with a full load can vary from 2 to 12 hours.
The relationship with Robojob is excellent. The service team responds in no time at all when we need help.
When I think about it now, I realize that we should have made this decision much earlier. In the beginning we had doubts about the installation of a robot on an existing machine. Consequently, we decided to wait a little longer before purchasing a robot. But in the end we made the decision and installed a robot on an older machine that also does great work. The output from this machine has since doubled while the operator now has more time.
Our employees are also extremely happy with the robots because they take over the physically demanding, routine tasks from them. This gives them more time to focus on important tasks such as preparing the machines and quality control. The robots aren’t there to cut back on the workforce; on the contrary, they’re enabling us to increase production and to make work more pleasant for the operators. All employees experience this as very positive."
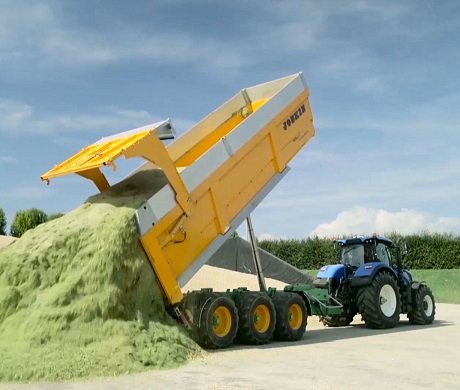