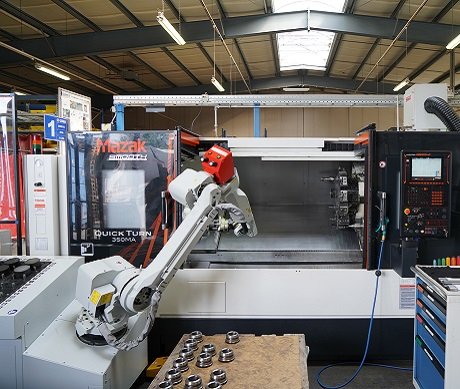
Durwen Maschinenbau GmbH
Durwen produces fork positioners or clamping forks, rotating turning equipment and many other variants.
Durwen Maschinenbau GmbH
Durwen produces fork positioners or clamping forks, rotating turning equipment and many other variants.
Durwen Maschinenbau GmbH is a medium-sized, third-generation family business. The company was founded in 1946 and has been manufacturing forklift truck attachments since the 1970s. Durwen produces fork positioners or clamping forks, rotating turning equipment and many other variants.
It has always been company policy to ensure a high level of internal value creation. This applies particularly to the machines used in the production department. By virtue of the well-equipped machining department, Durwen is able to produce high-quality components while ensuring excellent delivery times. In a global market, it is of course important to focus on the economic health and profitability of the business. For this reason, Durwen has made significant investments in automation. One of the building blocks of this project was the collaboration with RoboJob.
Klaus Durwen, business manager: “We manufacture various series of turned components for our own products. We wanted to automate these recurring turned components, which are manufactured in quantities of 100 to 500 pieces. This is the only way to profitably produce these parts. That’s why we started looking for solutions for the automation of our lathe.
Mr. Wall, our production manager in the field of turning technology, came across the company RoboJob on the internet. We then got in touch and Mr. Detlef Scholz from RoboJob's field staff paid us a visit in December 2019. For the automation of our Mazak machine, Mr Scholz made sure that he was accompanied by the Mazak representative. They know each other well. During our meeting, we immediately had the right people around the table.
When thinking about investing in new technologies, such as automation, it’s important to consider all aspects of the investment. We were highly impressed with the robot's simple programming. When switching to a new component, we were amazed just how easy and fast it was possible. RoboJob's software is very user-friendly and logical. When we also visited the workshop of RoboJob's sister company in Belgium, we could also see where this company comes from. The concept proposed by RoboJob with the promised short changeover time of the robot and the visit to the factory in Belgium convinced us.
We then decided to automate our Mazak QT 350 MA with a RoboJob Turn-Assist Essential i. The entire process went smoothly in spite of the corona crisis that had occurred in the meantime. The project management of RoboJob, the field sales employee Mr. Scholz, our department manager Mr. Wall and the Mazak company were in constant contact with each other. This way, all technical requirements were met.
The Mazak company installed a robot kit to ensure the communication between robot and lathe. During delivery, installation and commissioning, everything went according to plan. Within a week the robot was ready for use, including the doors’ automation. We were immediately able to produce our components.
What impressed me the most is that we were immediately able to use the robot and start production. I know this is often promised, but RoboJob really made it possible. Actions speak louder than words.“
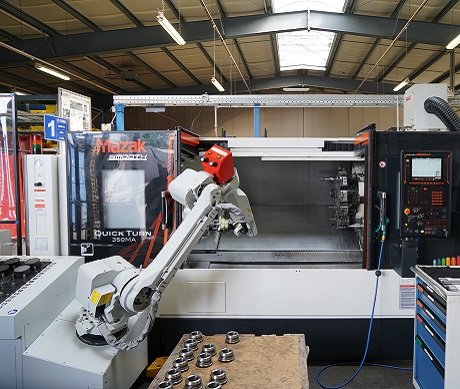