
Bopla Gehäuse Systeme GmbH
The BOPLA company, located in Bünde, just north of Bielefeld, is one of the key producers of electronic housings.
Bopla Gehäuse Systeme GmbH
The BOPLA company, located in Bünde, just north of Bielefeld, is one of the key producers of electronic housings.
For more than 50 years, the company has been developing and producing highly specific electronic housings in plastic and aluminium. Bopla has been part of the international Swiss group Phoenix Mecano AG since 1977. The housings that Bopla makes are used in, among other things, measurement and control technology, in machine construction and also in the medical industry.
Mr Michael Schmidt, Technical Manager: “It is our business philosophy to get as much return from every machine as possible. The spindle has to run for as many hours as possible, preferably 24hrs a day. However, working in 2 or 3 shifts is very expensive, so we started looking at the possibilities of automation.
In other locations, some colleagues had already tried to build a solution themselves using an industrial robot. They would then have been working on it for half a year before this effective solution came up. An additional problem was that it was very difficult to switch from one product to another. After all, you need a lot of robot knowledge before you can get started with such a robot. This was the reason for us to look for an existing standard solution with user-friendly programming.
We arrived at RoboJob via Hoffmann and Mazak. With the experiences of the other locations in mind, simple programming was particularly important to us. And RoboJob also convinced us about that.
In June 2018, our first Mill-Assist Essential was installed on a Datron CNC machine. That was an existing machine, which had been used in our production department here for a number of years. It did have an interface, but in a very closed software version. For both RoboJob and Datron, this was the first time that a Datron machine was equipped with a robot. It was logical that it took a bit of searching at first, but after a few weeks all the question marks had been removed. Since then, the robot has been running flawlessly and there’s been no problem whatsoever.
This summer a second system was added, this time to a new Haas machine: a Haas V2ss was equipped with a Racks system from RoboJob. This installation already went much more smoothly, and this time everything was done in one week. A Mill-Assist Essential has therefore also been added in our branch in Hungary, again on a Datron machine. This installation too went much more smoothly than at our Datron unit in Bünde. So you can see that progress is being made, and that lessons are being learned from previous experience.
In our production we have to produce a lot of different products with our machines, and therefore switching from one product to another is very important. Using RoboJob automation, that goes extremely quickly, not only thanks to the software, but also thanks to the flexible table. You can configure that table quickly and easily, so that you can place both small and large pieces on it.
So now there are 3 RoboJob systems active in our company. Our goal was to significantly increase production capacity, and we succeeded in that. We produce with a lot of man-free hours on these 3 machines. The operator who operates the robot also operates a second machine. Apart from increasing our capacity, it’s also striking how quickly these robots can be deployed. An installation is now finished in a week and our people have already been trained. This means they can immediately start working with the robot, and this is exactly what they do. Because we now get more hours out of the machine, we are also able to sharpen our prices in the market and we’re receiving more orders. Mission accomplished!
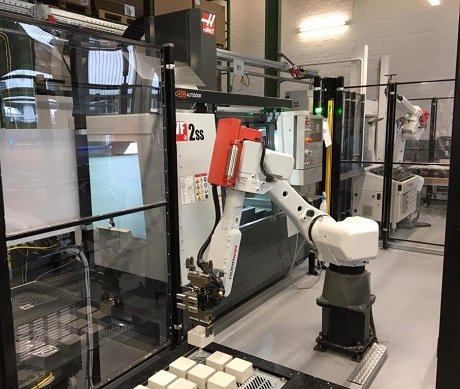