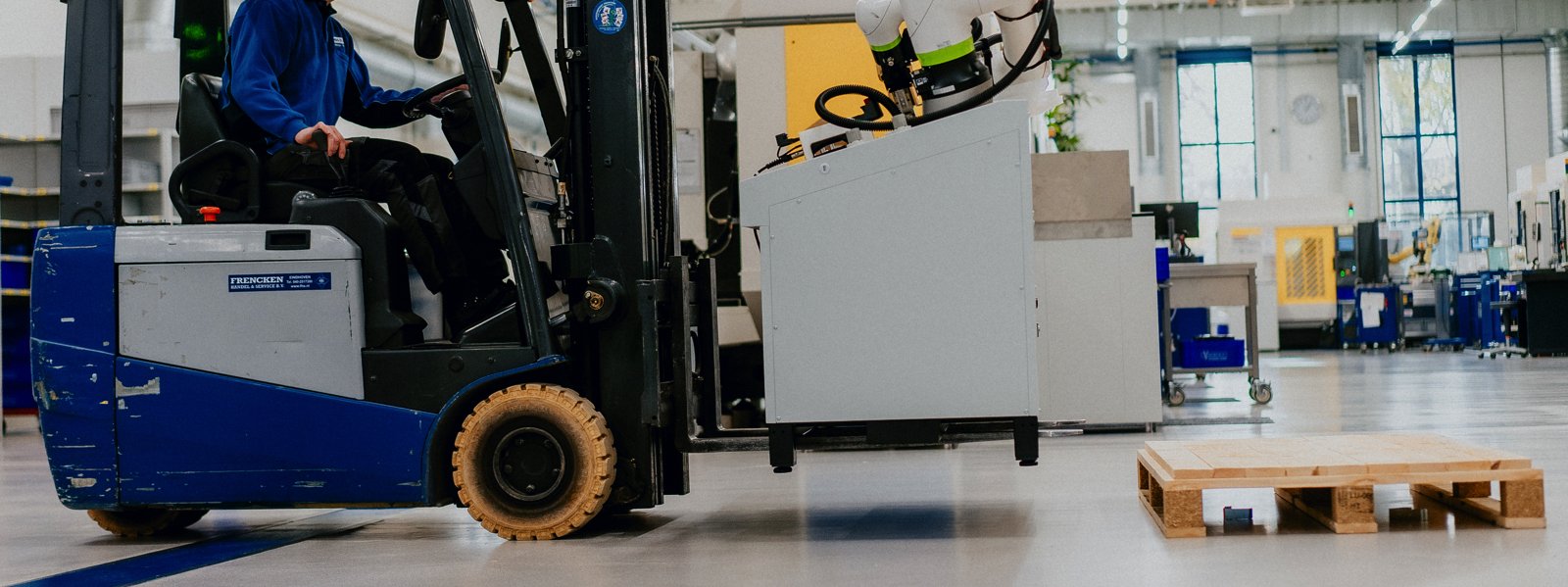
Vedos Verspanende Techniek welcomes first Coby CNC
Vedos Verspanende Techniek welcomes first Coby CNC
Flexible solution
Peter van Dijk and Jos Beumers had been looking for a flexible automation solution for some time. Ideally a robot or cobot that could go back and forth between a Fanuc milling machine and a DMG Mori lathe. Another requirement was that it needed no cage or fencing, and that the programming was simple. “During a visit to FANUC Benelux, we were introduced to the new CRX cobot, and we kind of liked it,” says Peter van Dijk. “Jos and I were actually planning to order one and get to work with it ourselves. Until we heard from Bert Versteeg, Sales Manager at our machine supplier Humacs Krabbendam, that RoboJob was already building a system with the CRX cobot.”
“We were introduced to Coby CNC, RoboJob’s latest development, through Humacs Krabbendam. We went to take a look at RoboJob and got a demonstration of the prototype. It turned out to be exactly what we were looking for: a cobot that you can shuttle between different machines, that is quick and easy to set up and completely accessible without extra fencing or scanners. Moreover, we liked the 'do-it-yourself' principle, because Jos and I are quite skilled in that kind of stuff. We love to innovate and are always looking for a new project that can take our production to the next level.”
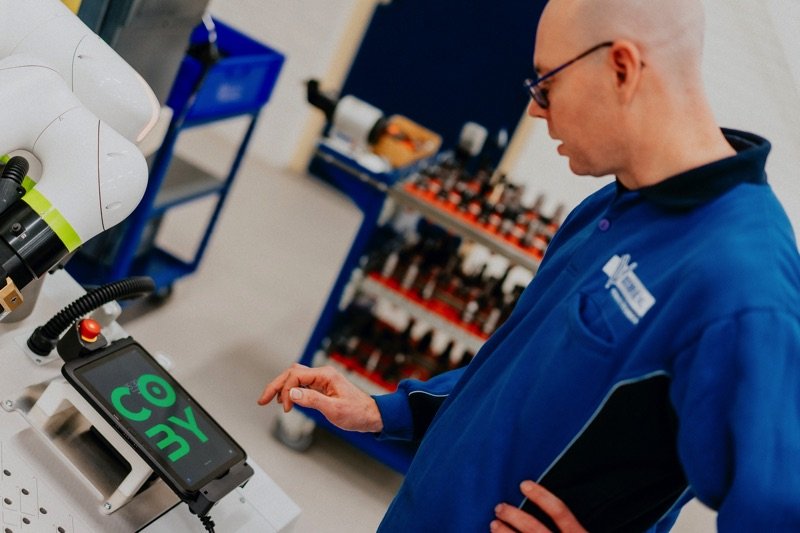
A learning process
The installation is now complete. For the RoboJob Research & Development team, this was an important step in the development of Coby CNC. Coby's goal is to make automation completely DIY and extremely accessible. That is why it is important to listen carefully to the first customers, even more than usual. It is then up to the R&D team to address the suggested improvements and smooth out the installation process.
“The installation went as expected,” says Jos Beumers, CNC operator at Vedos. “There were some bumps in the road that could have gone better. We discussed them with the Coby team and they’ll be addressed. But aside from that, things went smoothly.” The team is positive about the collaboration. “It is very inspiring and interesting for us to think along with a customer about what we can improve,” says Zeno Gillis, Software & Robotics Engineer at RoboJob. “It is important that the first Coby systems go to customers who want to think along with us and are open to a learning process. It’s a great way for us to tailor the system to the end user.”
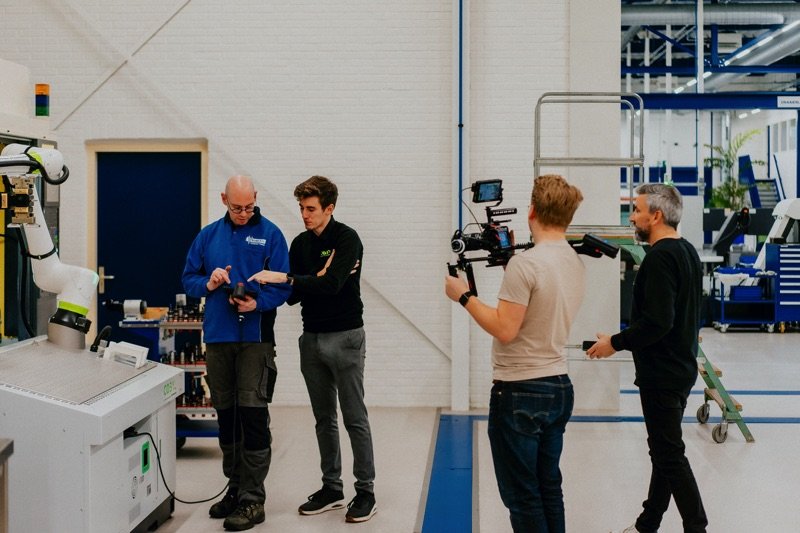
Quiet on set!
RoboJob’s Marketing Department was quite involved in the installation as well: Vedos' workshop had to double as a movie set for two days. The Coby website will soon feature an online platform, including short video tutorials that guide the user through the entire installation process. That’s why the process was filmed from A to Z. “The filming slowed down the installation considerably, and we are very grateful to the people at Vedos for allowing us to film in their workshop,” says Marketing Manager Steven Craenen. “With all the pictures and videos, our marketing team can realize quite a few things, from which customers reap the benefits.”
Since being installed in November, Coby has fully integrated into Vedos Verspanende Techniek. “You can tell he’s still a rookie,” Peter van Dijk jokingly says. “But we knew we would be the first to work with Coby, and it’s actually going amazingly well. Occasionally we still run into a 'bug' or problem, but RoboJob solves them quite quickly. Everything else, we can manage ourselves. We got the hang of programming after a few days. It is actually much simpler than I had previously thought. If you can operate a turn or mill, working with Coby is child’s play!”