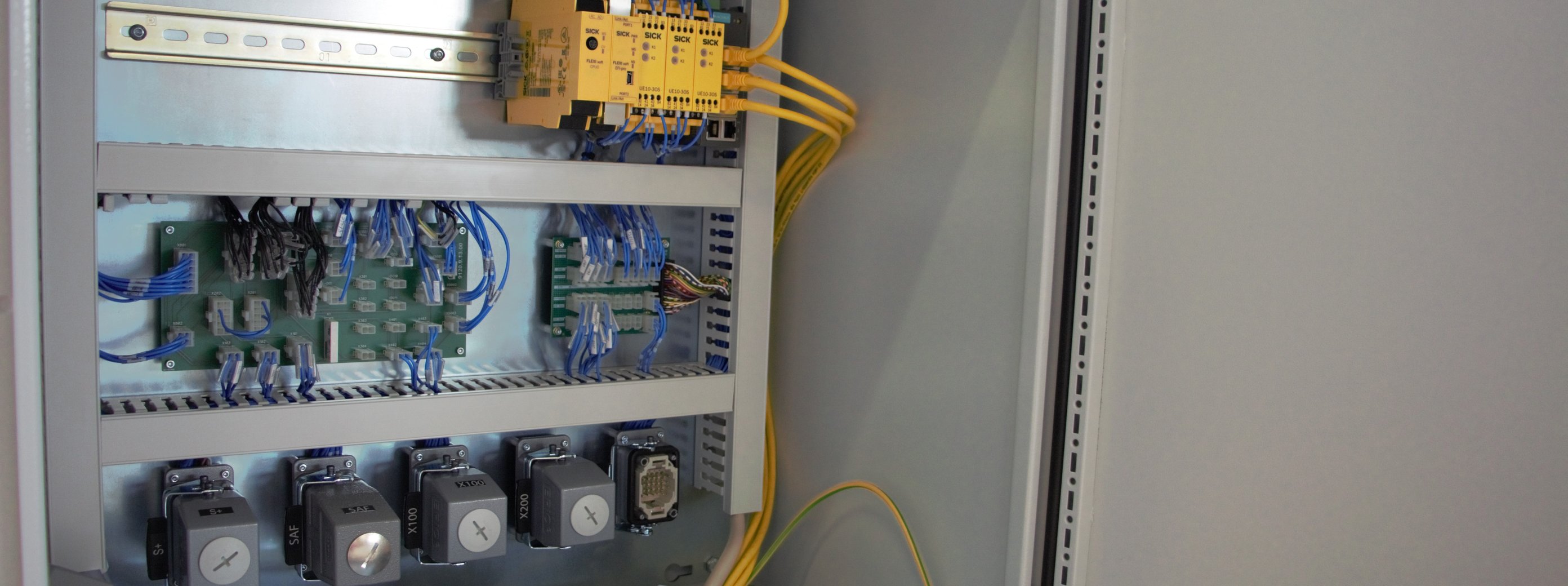
RoboJob is fully focused on the automation of existing machines
RoboJob is fully focused on the automation of existing machines
This has been a noticeable trend for a few years now: small and large CNC machine manufacturers offer their CNC machines in combination with CNC automation. It allows the CNC machine manufacturers to offer the customer a total package. However, there are thousands of existing CNC machines throughout Europe without automation, and RoboJob wants to do something about that.
For more than 12 years, RoboJob has been working on the most extensive portfolio of standard CNC automation solutions. The Turn- and Mill-Assist Series have become the standard in CNC automation, and with the Racks and especially the Tower, RoboJob now has a solution for every customer. It’s striking that the Belgian CNC specialist not only automates new machines, but existing machines in particular.
“It’s often a misunderstanding that exists in our market: a robot can only be placed on a new machine with a robot interface and an automatic door," says CEO Helmut De Roovere. “Nothing however, is further from the truth: of course we have to be able to communicate with the machine in order to exchange signals, but it’s not that exciting. Every machine has the necessary signals to make this communication possible. In the meantime, we have now built up significant experience with more than 700 installations of scores machine brands ‘in the field’. Most of this on existing machines.”
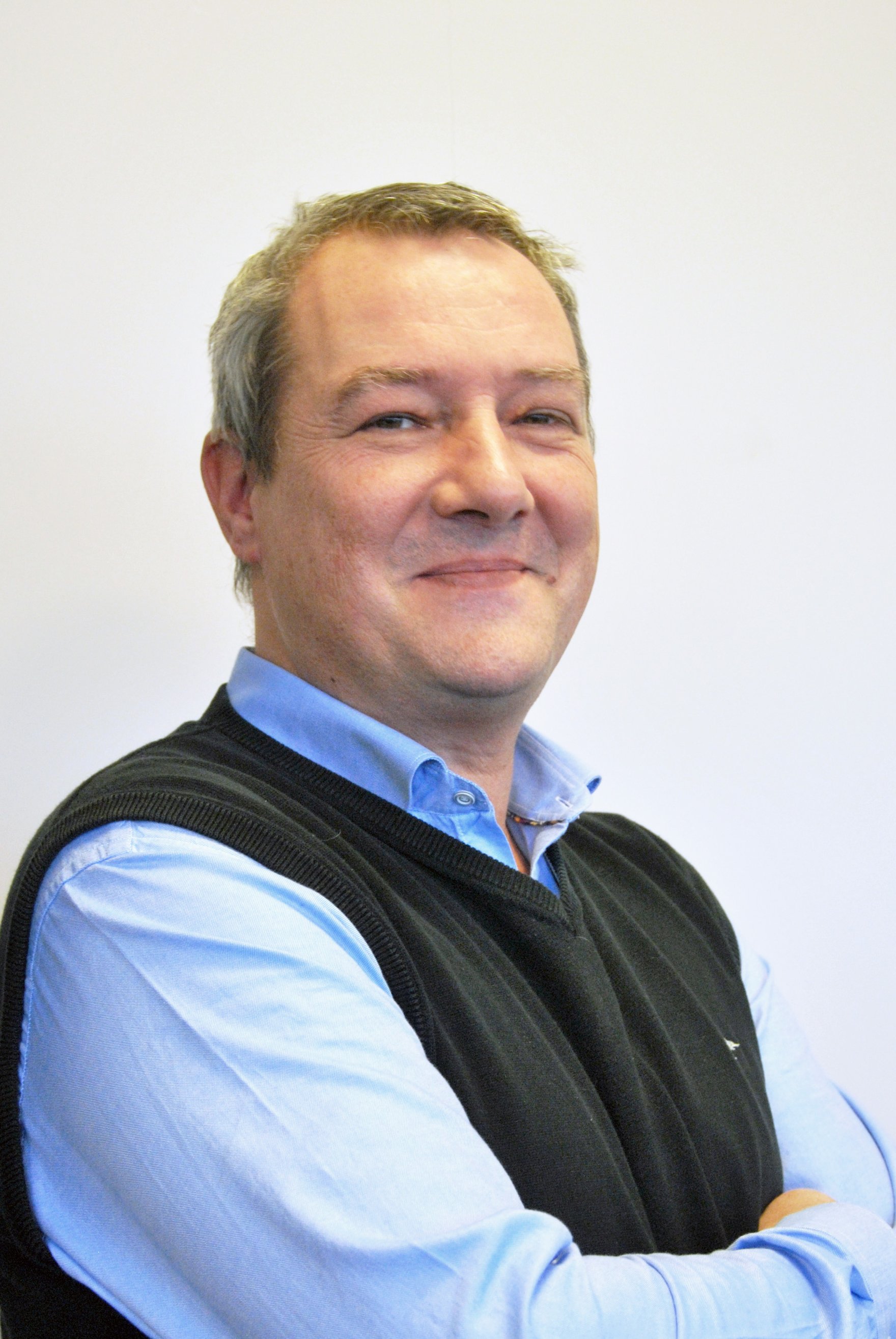
De Roovere finds it a rather positive trend that more and more new machines are being offered with robot: “It confirms the need to focus on automation. It’s really useful for the customer to buy everything from one source. And there’s a lot of profit and efficiency still to be gained from the automation of existing machines.” The CEO speaks from experience: at RoboJob's sister company 7 machines have already been automated, including existing machines. “Those machines are already there, but without automation they’re also too often idle. We now sometimes already use the robot for 5 pieces. For example, if the cycle time is 20 minutes, this gives the operator almost 2 hours to prepare another machine or to make single pieces. And the machine with robot gets more spindle hours, and that’s ultimately what it's all about.”
Thanks to the robot, existing machines will also yield more returns, they will be paid back faster and they will generate more money.