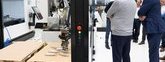
A look to the future: AI vision technology in industrial automation
A look to the future: AI vision technology in industrial automation
At RoboJob, we are constantly striving to take the automation of production processes to the next level. With the introduction of our pioneering AI vision technology, optionally available on our new 'Pallet-Load Integrated', we are taking an important step in this regard. By giving our robots "eyes", we unlock a range of new possibilities for industrial automation. In this blog post, we explain this innovative solution and discuss the role of our internally developed AI.
Why do our robots need "eyes"?
Industrial robots excel at performing repetitive tasks under predictable conditions with high accuracy. Traditionally, they are therefore used for fixed production processes and large series. However, today's industry demands more flexibility: smaller to medium-sized product series and frequent changeovers require a different approach.
Smart, user-friendly software enables robots to calculate movements based on parameters, allowing them to be quickly converted to new products. Yet existing solutions continue to rely on mechanical aligneers to position workpieces precisely. Every product change requires time-consuming and costly adjustments, limiting flexibility and creating extra work for the operator.
Moreover, without visual feedback, robots cannot detect if workpieces are incorrectly positioned. Nor can they distinguish between different workpiece types and processing conditions. This can lead to errors, unplanned downtime and loss of valuable production time. By providing robots with visual intelligence - giving them "eyes", so to speak - we significantly improve both flexibility and reliability.
The role of our AI
Adding "eyes" to robots is no easy task. Traditional camera systems are often expensive, bulky and sensitive to environmental factors such as light, reflections and lack of texture. Moreover, they require complex setup work, limiting their advantage over mechanical systems.
Our internally developed AI technology provides a solution in this regard. Instead of complicated configurations, our system only requires a CAD file of the workpiece. Our AI, trained on a wide range of images, can effortlessly recognise a variety of shapes and materials - including reflective and textureless metals. This eliminates labour-intensive setup work and makes the system extremely user-friendly.
One step closer to full autonomy
Thanks to visual intelligence, our robots become more resilient to variations in the position of workpieces. This simplifies integration with other autonomous systems, such as mobile robots. These can automatically supply and remove workpieces, for example from standard wooden europallets, without the need for human intervention. This reduces the physical strain on operators, minimises downtime and increases productivity.
What does this mean for our customers?
In short: shorter set-up and changeover times, more flexibility, a more stable production process and increased efficiency. Thanks to robust performance under a variety of conditions, including varying light conditions, reliability remains high. The system can be used for various product types and materials with minimal effort, without complex adjustments.
We are extremely proud of this technological breakthrough and look forward to using it to support our customers in their quest for a more flexible, efficient and future-proof production environment. Keep following us for more updates and discover the possibilities that AI-driven automation can offer you.